Rubber Gloves
Research group: professor Alex Routh
The Problem
Billions of rubber gloves are manufactured every year, through a production process which is extremely energy intensive.
Work Needed
We need to better understand the many aspects of the glove manufacturing process in order to consider how the environmental impact could be reduced.
Our Work
We have been modelling different stages of the production process to improve this understanding.
Background
Every year approximately 300 billion thin rubber gloves are made, often in Malaysia. These are used in laboratories, hospitals, food preparation and many other settings.
Each glove is made by dipping a hand-shaped mold into a concentrated electrolyte solution, drying and then dipping into a latex solution with about 10% solids. To obtain a thin final film, a large amount of water is used in the initial stage to dilute the latex. At the final stage of production, this water is evaporated with a high energy cost. The energy requirement of evaporating the water component is large (2.4 x 10 16 J). This corresponds to around 2% of the UK’s total energy use – just for boiling water!
Despite its industrial importance, many aspects of thin glove manufacture are not yet understood. The application of a better understanding could reduce the environmental impact of the process.
Our Work
We are modelling the production process to better understand the formation of latex gloves. We are also examining how strength evolves in the drying product. If we can increase the solids content in the latex bath then we can reduce the amount of water which needs to be evaporated.
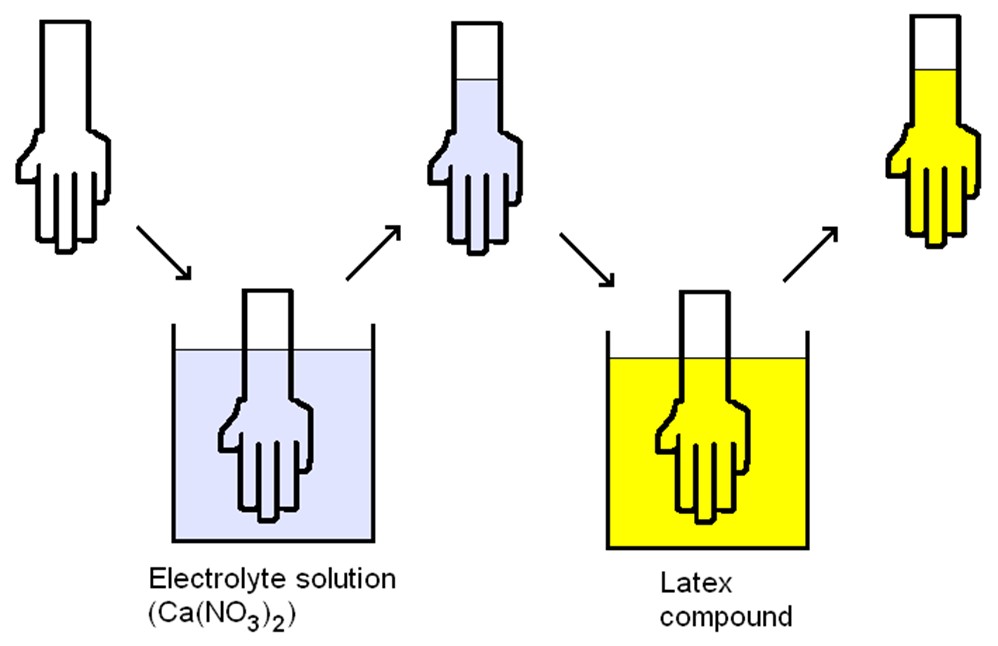
The method of manufacture involves taking a ceramic former and dipping it into a solution of electrolyte, typically calcium nitrate. The coated former is dried and then dipped into a bath of dilute, aqueous polymer latex. The calcium nitrate (called coagulant) causes the latex particles to aggregate onto the former, forming a weak, water-containing film described in the industry as wet gel. Upon removal and subsequent drying the film transforms into the glove, which is then removed from the former and packaged. We sketch the process in the figure.
Publications
Robert Groves and Alexander F. Routh, Film formation during the coagulant dipping process, Journal of Polymer Science: Polymer Physics 55(22): 1633-1648 2017.
Robert Groves, Patrick Welche and Alexander F. Routh, The coagulant dipping process: Investigations of former motion effects and coagulant loss into the dipping compound, Soft Matter 19: 468-482 2023.